When planning any type of construction, one of the most critical yet often overlooked factors is the bearing capacity of the soil. Whether you’re building a small garden shed or a multi-storey commercial complex, understanding how well the ground can support the weight of your structure is key to ensuring long-term safety and stability.
This blog breaks down the concept of soil bearing capacity in simple terms, explores why it’s important, and walks you through how it’s measured, what affects it, and how it can be improved.
What Is the Bearing Capacity of Soil?
In basic terms, bearing capacity refers to the maximum load per unit area that the ground can support without experiencing failure. Think of soil as the silent supporter of every building — it must hold the entire structure above it. If it can’t handle the weight, the consequences can range from minor cracks to major structural instability.
For example, a lightweight timber garden house might be built safely on compacted soil with a shallow foundation. But a heavy concrete apartment complex needs deep foundations reaching stronger soil layers to avoid uneven settlement.
The bearing capacity helps determine what type of foundation is needed, how deep it should go, and what building techniques are most suitable for the site.
Why Is Bearing Capacity Important?
Soil bearing capacity plays a central role in the success or failure of any building project. Here’s why it matters:
Structural Integrity: A weak or unstable foundation causes stress to be unevenly distributed, which can lead to cracks in walls, buckled floors, or leaning structures.
Safety: Buildings constructed on inadequate foundations pose safety risks for occupants and nearby properties.
Cost-Effectiveness: Early knowledge of the soil’s capacity allows for smarter planning, potentially reducing costs associated with deep foundations or soil replacement.
Design Considerations: Engineers can design appropriate foundations suited to the specific ground conditions.
Regulatory Compliance: Most building regulations require site investigations to assess soil conditions before permits are granted.
In short, understanding the bearing capacity of the soil is a fundamental step in any responsible construction plan.
Types of Bearing Capacity
Understanding different types of bearing capacity helps clarify how decisions are made during foundation design:
Ultimate Bearing Capacity
This is the maximum pressure the soil can withstand before failing. It reflects the breaking point of the ground and is generally not used directly in construction due to the lack of a safety margin.
Net Bearing Capacity
Net bearing capacity subtracts the existing pressure from the soil’s own weight (overburden) from the ultimate capacity. This gives a more realistic measure of the soil’s ability to support additional loads.
Safe Bearing Capacity
This is the most important value used in construction. It’s the maximum pressure that can be safely applied to the soil without risking failure. It includes a factor of safety (typically between 2.5 and 3) to account for natural variations and uncertainties in the soil.
By working with the safe bearing capacity, engineers ensure that foundations remain stable even under unexpected conditions like extra loads or heavy rainfall.
Factors Affecting the Bearing Capacity of the Soil
Many interrelated factors influence the bearing capacity of soil:
Soil Type: Different soils behave differently. For instance, dense sandy soils offer high bearing capacity, while loose silt or expansive clay has much lower strength.
Moisture Content: Wet soil can become soft and unstable. Clay, for example, can hold water and expand, reducing its ability to support structures.
Foundation Depth: Deeper foundations often reach more compacted and stable soil layers that provide better support.
Load Type and Distribution: Point loads (from columns) versus uniformly distributed loads (like floor slabs) impact how the soil behaves.
Soil Compaction and Density: Well-compacted soil provides higher bearing capacity due to fewer air gaps and better internal friction.
Presence of Organic Matter: Soils rich in peat or organic content are usually compressible and have very low bearing capacity.
Slope and Topography: Building on sloped ground introduces lateral forces and increases the risk of sliding or movement.
Soil assessment must consider all these factors together to arrive at an accurate and reliable bearing capacity estimate.
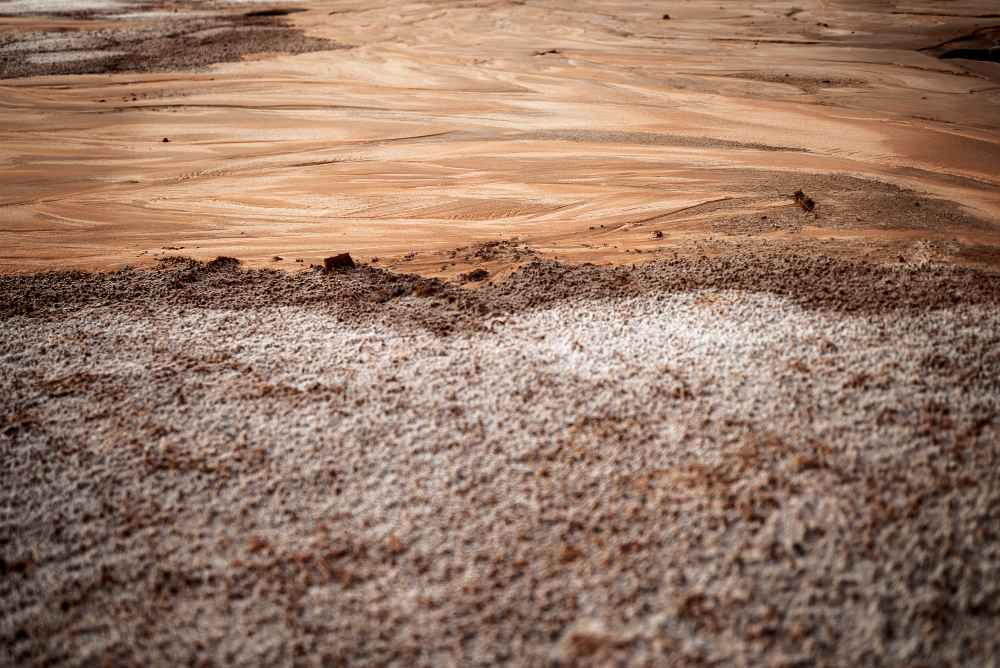
How Is Bearing Capacity Measured?
Determining soil bearing capacity involves both on-site tests and laboratory analysis. Here are some of the most commonly used methods:
Site Investigation
- The first step involves geotechnical engineers drilling boreholes or excavating trial pits.
- Samples are collected at different depths to identify soil layers and characteristics.
Standard Penetration Test (SPT)
- A widely used field test where a hammer is used to drive a sampler into the soil.
- The number of hammer blows gives an idea of soil resistance.
- More resistance generally indicates stronger soil.
Plate Load Test
- A steel plate is placed on the soil and gradually loaded.
- Engineers measure how much the plate sinks under each load.
- It provides direct insight into how the soil will perform under real building loads.
Laboratory Testing
- Soil samples are tested for strength, moisture content, density, and other properties.
- Helps verify field results and understand specific behaviours.
These tests ensure that construction decisions are based on accurate, site-specific data.
Safe Bearing Capacity for Various Soils
Different soils have varying capacities to support structural loads. Below are typical safe bearing capacity values (in kilonewtons per square metre) for a wide range of soil types. These values are intended for general guidance and must be verified through professional site-specific investigations.
Cohesive Soils (Clays and Silts)
Soil Type | Safe Bearing Capacity (Kn/M²) |
Soft Clay | 75 |
Medium Clay | 150 |
Stiff Clay | 300 |
Very Stiff Clay / Hard Clay | 400 |
Silt (Loose) | 100 |
Silt (Compact) | 200 |
Cohesionless Soils (Sands and Gravels)
Soil Type | Safe Bearing Capacity (Kn/M²) |
Loose Sand | 100 |
Medium Sand | 200 |
Dense Sand | 300 |
Gravel (Loose) | 250 |
Gravel (Well Compacted) | 450 |
Sand And Gravel (Compact) | 400 |
Fills and Others
Soil Type | Safe Bearing Capacity (kN/m²) |
Compacted Filled Ground | 150 – 300 |
Black Cotton Soil (Dry) | 100 |
Black Cotton Soil (Wet) | 50 |
Boulder With Stiff Clay Matrix | 450 – 600 |
Rocks and Rocky Soils
Soil Type | Safe Bearing Capacity (kN/m²) |
Soft Rock | 400 – 800 |
Laminated Rock | 800 – 1500 |
Weathered Rock | 600 – 1000 |
Hard Rock (E.G., Granite) | 1000 – 3000+ |
Understanding these values helps determine the appropriate foundation type and whether soil improvement measures are needed. For instance, building on soft clay typically requires deep foundations or reinforcement, while hard rock can often support structures with minimal foundation depth.
Always consult with a professional engineer before making design decisions based on these values.
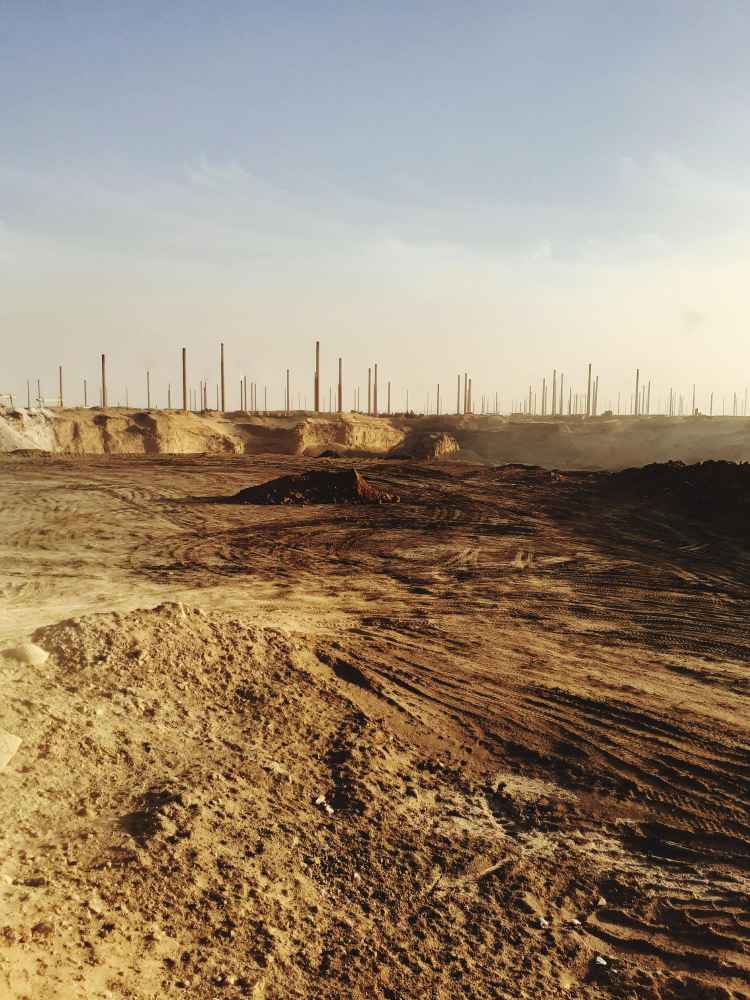
Improving Soil Bearing Capacity
Sometimes the natural bearing capacity of a site is insufficient. Thankfully, several engineering techniques can improve the soil:
- Compaction: Using rollers or vibration machines to densify loose soil.
- Soil Replacement: Removing soft or compressible soils and replacing them with stronger fill.
- Reinforcement: Installing geotextiles, stone columns, or compacted gravel to increase stability.
- Stabilisation: Mixing soil with cement, lime, or other additives to harden it.
- Drainage Improvements: Installing proper drainage systems to prevent water accumulation.
- Use of Piles or Piers: Transferring loads to deeper, stronger soil or bedrock layers using driven or bored piles.
Improving the soil can make an otherwise unusable site suitable for development.
Common Signs of Poor Bearing Capacity
Recognising the symptoms of soil-related problems can help you intervene early. Some common warning signs include:
- Cracks in Foundation or Walls: These may appear shortly after construction or worsen over time.
- Uneven Floors: Sloping or bouncy floors may suggest differential settlement.
- Doors and Windows Sticking: Misaligned frames or difficulty opening/closing can be a subtle sign.
- Water Pooling Around the Foundation: Poor drainage can soften soil and reduce capacity.
- Visible Tilting or Sagging: A clear sign of inadequate support or soil movement.
If these signs are visible, it’s essential to have a professional inspection.
When Should You Worry About Bearing Capacity?
You don’t need a geotechnical survey for every minor project, but in the following situations, a soil assessment is critical:
- Home Extensions or Additions: Adding floors or rooms changes the load distribution.
- Building on Slopes or Near Water Bodies: These conditions often have unstable or varied soil profiles.
- Converting a Property: Changing a residential space to commercial use may require load reassessment.
- Historic or Older Buildings: Foundations built decades ago might not meet today’s standards.
- Signs of Past Issues: Cracks, repairs, or sloped floors are red flags.
- Heavy Structures: Projects like swimming pools, retaining walls, or underground garages require careful planning.
Role of a Construction Company
A trusted construction company plays a vital role in managing the bearing capacity aspect of your project. Here’s how:
- Site Coordination: Works with geotechnical engineers to plan and execute soil testing.
- Foundation Design: Chooses the right foundation type and depth based on the soil’s capacity.
- Problem Solving: Suggests practical and cost-effective solutions if the soil conditions are less than ideal.
- Regulatory Compliance: Ensures that all foundation and structural plans meet local building codes.
- Quality Assurance: Oversees that soil improvement works are done correctly and inspected as needed.
Choosing the right construction partner ensures peace of mind from the ground up.
Conclusion
The soil beneath your building is just as important as the materials you use to construct it. Understanding and addressing soil bearing capacity ensures that your building is not only structurally sound but also safe and long-lasting.
Neglecting this step can lead to costly repairs, regulatory issues, or even structural failures. Fortunately, modern engineering practices and professional guidance make it easier than ever to work with the ground you have.
If you’re planning a new construction project, extension, or simply want to ensure your property’s foundation is safe, get in touch with our expert team. We offer site assessments, soil testing coordination, and tailored foundation solutions.
Let’s build on solid ground – together. Contact us today for a consultation.
Frequently Asked Questions !
Can I build on clay soil?
Yes, but you must consider its expansion and contraction with moisture changes. Proper foundation design and drainage are crucial.
Who checks the soil before building?
A qualified geotechnical engineer or engineering geologist performs the soil investigation.
How long does a soil test take?
Basic tests can be done in a day or two on-site, while full lab results may take one to two weeks.
Is soil testing expensive?
Costs vary based on site size and complexity but generally range from a few hundred to a couple of thousand pounds. It’s a smart investment considering the risk of future repairs.
What if the soil is not good enough?
Don’t worry. Most soil issues can be addressed through engineering solutions like soil replacement, compaction, or using piles.